
前回のKTCインタビュー「壊れ方の美学」に続き、今回は「ネプロス誕生秘話」を紹介させていただきます。チームの中心となり企画段階から開発全般に携われていた寺嶋様から、お話を伺って参りました。
「ネプロス誕生秘話」インタビュー

京都機械工具株式会社
T&M推進本部 商品開発部 部長
寺嶋 朗様
――寺嶋様のご経歴と、ネプロスの始まった経緯をお話しいただけますか。
私は入社した時は商品開発だったのですが、 当時は新しい事業を行っていた別の部署に所属していました。それが、ネプロスを始めることをきっかけに商品開発に戻り、チームに参加させてもらうことになりました。
そして、ネプロスを発売したのが1995年になります。その3年前から、市場調査や新しい材料の研究、新しい加工技術を使っていこうといった経緯で、匿名チームとしてプロジェクトがスタートしています。
―― ネプロスのコンセプトはどのように決まったのでしょうか。
コンセプトは「より強い・より使いよい・より美しい」になります。今まで工具の見た目で「より美しく」という発想はほとんどなかったのですが、ネプロスではデザイン面も優れたものにしていこうとなりました。
デザインも見た目だけではなく、機能美。「これまでにない、機能をデザインしよう」というコンセプト、つまり機能性をデザインに反映させていくという発想でスタートしました。
製品でいいますと、例えば、T型ハンドルではハンドルの真ん中を削ることによって非常にすっきり見せているのですが、その真ん中を削ることによって早回しする際、非常に優れたフィーリングを生み出すことに繋がっています。
他には、ラチェットでは"コンパクトヘッド"というのを謳っていて、もちろんコンパクトではあるのですが、実際の外径よりも見た目をさらにコンパクトに見せるため、横の丸みの芯をわざとずらしています。そうすることで、上から見たときに、よりコンパクトに見えるようになっています。こういった発想は過去にはなくて、ネプロスから取り入れています。
―― 過去にミラーツールという製品がありましたが、それはネプロスの前身になるのでしょうか。
そうですね、ミラーツールは元々KTCにあった工具を磨いただけの製品でした。磨きもそこまで極めておらず、とにかく磨いて光らせた製品です。
それではダメだろうと。海外から優れた工具が入ってきた時期でもあったので、それらに対抗して、機能も見た目も優れた世界一の工具を作るという決意でネプロスを始めました。
―― 材質自体も全然違うものになるのでしょうか。
そうですね。製品によるのですが、変えています。もし、同じ材料だとしても、熱処理を変えたりメッキを変えたり、後工程を変えることによって仕上がりに大きな違いを出しています。
ネプロスの場合は小ロットで作っているので、工程を細かく変えやすいといった面もあります。
―― ロットのボリューム感はどれくらいの違いがありますか。
通常の汎用工具で何千といったロットで作っているものが、ネプロスだと50とかになります。
ネプロスは段取りだけでも結構な工程が必要なのですが、50個を作るために多くの手間隙をかけています。
―― それは工数も考えて、50しか作れないということでもあるのでしょうか。
ソケットのようにたくさん出る製品であれば200、300となるものもあるので、作れないということではありません。
また、後工程に磨きというのがあるのですが、これが非常に時間が掛かります。そのため、前工程でたくさん作っても後工程で詰まってしまうというのもありますね。結果的に、KTC工具と比べて圧倒的に少なくはなります。
―― 磨き工程も、普通の製品に比べて手間と時間を掛けられているのですね。
はい。磨きといっても、手磨きもあれば、バレルという石と研磨剤を混ぜて磨く場合もあります。その時間も最初は10倍程かけていました。今はかなり改善したのですが、それでも5倍くらいはかけていますね。
さらに、普通の製品だとバレルを流すだけの一工程で済むところ、ネプロスの場合は粗バレルをしてから仕上げバレルといった二工程に分けています。しかも、仕上げバレルの石や研磨剤も製品毎に合ったものを選んでいます。
―― ひとつひとつの材料を変えていくということは、準備自体にも時間がかかるということですね。
そうなんです。
代表作『NEPROS NBR390』について
それだけ工数をかけているネプロスですが、一時期伸び悩んだ時期もありました。しかし、NBR390というラチェットハンドルをきっかけにまた売り上げは伸びています。
私は商品開発の中核の方が営業に異動されたことを機に引き継いで、開発と設計を全体的に見ることになりました。そして、その前、私が最後に担当したのが390なんです。390が完成したので開発チームを移ったという経緯になります。
―― そうだったのですね。今でもネプロスを代表する製品としてお客様からも支持されていますね。
はい、完成するまでにとても苦労をしました。当初は「こんな高いものいらんやろ」「そんなの使っても一緒やろ」と言われることもあったのですが、「いやいや絶対に売れますよ、作らせてください」と経営会議で言いました。すると、作る方も追いつかないくらい売れたんです。
そして、このラチェットは未だに、機能的なクレームがほぼないですね。キズとか外観は多少はあるのですが、故障したとかのクレームはほぼゼロに近いです。
NEPROS NBR390 全長180mm 9.5sq.ラチェットハンドル ネプロス
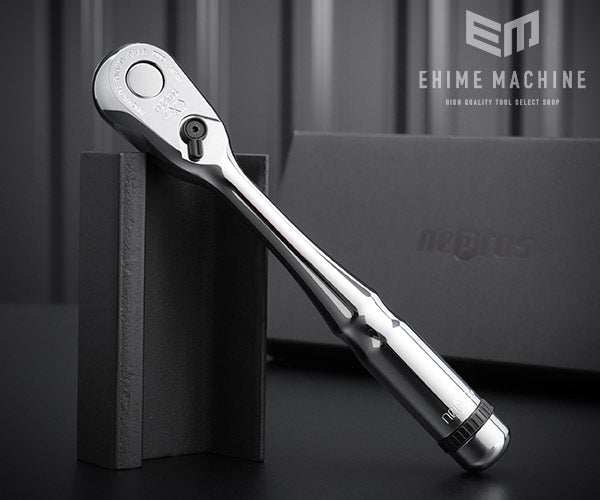
この製品は生産を終了しました。
―― 機能的な故障が少なくなった要因は何でしょうか。
設計と試験機ですね。
昔の試験をする設備では、例えばぐーっと力をかけていきガチャンと破壊したり、どれだけの強度なのか測ったり。または、ゆっくりと繰り返していき何回で破壊するかといった、実際の作業にありそうでないような評価しかできませんでした。
その後、実際の作業に即した評価をするための試験機を作りました。早回し試験機というのですが、ガッチャンガッチャンと早く回してトルクをかけていく機械です。そして、その試験機は力を加えるタイミングも微妙に変えられるんです。これによって、実際の作業で起こりがちな不具合を意図的に作れるようになりました。
ラチェットは、ギアと爪が噛み合う時、ゆっくりだとバッチンバッチンとスムーズに動くのですが、早回しするとちょっと先で引っ掛かったりします。それによって先が欠けてしまうこともありました。しかし、新しい試験機によって、これらの対策も講じられたので、現在の製品では先で掛かってグッと噛むような設計になっています。
―― ギアの角度とか山の角度ということでしょうか。
そうです。噛み合う時の角度ですね。
他社製品も徹底的に評価し、改善策を探しました。そこで改めて感じましたが、専門メーカー様はやはり優れた製品を作られていますね。
例えばドライバーを開発するとしても、総合メーカーの弊社でしたら、何年に1回のサイクルになります。しかし、ドライバー専門メーカーさんになると常にドライバー作られているので、きっちりとしたものを作られていると感じます。
また、昔はCADやコンピューター解析もありませんでしたが、設計と試験機の精度も上がったことによって、今では故障の少ない製品になっていますね。
――NBR390の開発期間はどれくらいですか。
最初の提案から、実際スタートするまでが半年くらいかかったと思います。納得してもらえるだけの情報を集めて資料を作ったりして、ようやくOKをもらえて。
それから、設計にも時間がかかりました。どんな機構にしようかといった構想からになりますし、機構も1種類だけだとうまくいかないので何パターンかの機構設計をしました。それを試作しながら、どの機構が一番優れているかと選定していき。そこから加工のばらつきであったり、お客様の使い方を想定していかなければいけません。
量産品は専用の機械がありますが、試作は機械がないのでほとんど手作りであったり、外注さんの精密な機械で作ったり。とにかく、費用と時間がかかるので、一回失敗するとまた次の試作を作るまでが大変で......その場合さらに、10日~2週間はかかってしまいます。
結局、試作期間もなんやかんや半年くらいはかかったと思います。 試作する時は、加工のばらつきが一番大きなパーツと、小さなパーツを組み合わせて試したらどうなるんだといったこともします。量産は公差の中でこれだけバラついてもいいとなりますが、試作品は公差のここを狙って作りましょうとなるので、普通の作り方ではなかなか作れません。
これらは、100分の1とか1000分の5といった精度で作る技術になるため、非常に大変ですね。
―― そこまで精密な作業を繰り返し、時間とコストも重なる中での失敗は、相当なストレスがかかるでしょうね......
うまいこといかなかったらどうしようという気持ちにはなっていきますね。費用と時間を使っていても、「いずれよくなる」と見えていたらいいですが、「いつまでたっても無理なんじゃないか」と先が見えない時は本当に寝られませんでした。
京都の繊細なものづくり
―― ネプロスのコンセプトでも使われている「より強い・より使いよい・より美しい」の”より”という言葉もありますが、際限ない高みを目指す精神、機能美を追求していく精神は、京都の伝統工芸に通じるものもあるのでしょうか。
以前はMADE IN JAPANということだったのですが、ネプロスあたりからMADE IN KYOTOと謳うことが増えました。京都の繊細なものづくりというイメージを出していければと思っています。
―― ネプロスをやりはじめて周りの反応が変わったというのはありますか。
昔は工具の取材なんてほとんどなかったのですが、今では数が増えましたね。また、ネプロスの検査をしている姿を取材されたり、「この職人によってこの美しさが生み出されている」といった内容で、現場に取材が行くようになりました。
例えば「世界一美しい工具は京都の職人さんが手をかけて磨いています」や、「部品同士がガタつきなく精密で繊細な加工を行っています」といったところをネプロスでは伝えていきたいですね。
――仕上げの面取りなど、限られた職人さんしか触れないという工程もありますか。
本当はそれではダメなのかもしれませんが、この人にしかできないという工程は実際にございます。
ただし、そのような工程がある一方で、ロボットを使って磨いていこうというチャレンジもしています。現在はロボットの性能も良くなっているので、人の目のように見た目を判断し磨き残しているところだけを磨いたりもできるようになりました。変則的な曲線部分も、昔は人の手でなければできなかったのですが今ではできつつあります。
―― 職人さんの技術と、テクノロジーの進歩を最大限に活かして製品を開発・製造されているということですね。海外からはどのような評価を受けているでしょうか。
アメリカやヨーロッパ等、海外の展示会に出展させていただいたこともあります。そこでも、非常に評判が良かったのですが、お値段を聞かれてびっくりされていました(笑)
以前はヨーロッパではバンに乗せて売っていたこともあるのですが、今ほどネットが普及していない時代だったので口コミで広まることもほとんどありませんでした。外国から来た知らないメーカーの商品が高いということで、実際に手にしてもらった時の評判は良かったとはいえ、爆発的に売れることはなかったですね。
ユーザーの声と開発者の想い
―― お客様からいただいた感想で嬉しかった言葉や、エピソードがあれば教えていただけるでしょうか。
そうですね。ネプロスは、ピカピカに磨いて綺麗な工具に仕上げてはいますが、「使い勝手がいい、この寸法じゃないと使えないんだ」と、ボロボロになるまで使っていただいてるのを見たときが嬉しかったですね。
もちろん、綺麗に飾っていただくのもとても光栄なことですが、開発に携わった人間としては使われるとやっぱり嬉しいです(笑)
夜中まで何回も何回もテストを繰り返して、うまく評価できなくてまた考え直したり。それだけ苦労して作った製品なので是非使っていただきたいという想いがあります。

―― ざっくりとした質問ですみません、寺嶋さんは開発のお仕事が好きですか?
開発は色んなお客様とお話しできますし、幅広い情報を先取りしないといけません。製品だけの情報だけではなく、物づくりの情報であったり、デザイン的な情報であったり。それに対して、やりがいがすごくありますね。
品質保証部にいたこともあるのですが、そこではお客様が使われた結果どうかという部署でもあり。その際、お客様の使い方がどうなのかといったことは開発部で知ることができましたし、経験が役に立ちました。
―― 製品が出来上がった瞬間のお気持ちはどのようなものでしょうか。
もちろん嬉しかったのですが、すごく心配でしたね。この製品、本当に世に出しても大丈夫なのかと。
試作品でうまくいっても、その後、量産品の段階でトラブルが起こるということも結構あるんです。そのため、量産品をテストするときも、ものすごくドキドキしますね。そして、それがうまくいったとしても、お客様の手元から戻ってきたらどうしようと。そのため、完成してからも嬉しいより心配の方が大きかったです。
―― なるほど......心から安心できるとしたら、お客様の手元に届いて、一定期間クレームもなく、良い感想が戻ってきた時になりそうですね。
そうですね。それまでは時間がかかるので、1ヶ月くらいでは安心できないかもしれないですね。一定の評価をいただけたらようやく安心できますが、それまでは本当に心配で。
―― 普段手にしている製品がどのようなご苦労と想いによって作られているか、その一端を知ることができました。本日は誠にありがとうございました。
ありがとうございました。
インタビューを終えて
販売店として、製品の詳しい性能を教えていただく機会はあるのですが、今回のように開発ストーリーを0からお伺いする機会は多くありません。寺嶋様のお話と、前回の記事「壊れ方の美学」を通して、普段販売している製品が、どれほど追い込まれた末に完成し、世の中にリリースされているかを知ることができました。
機能美が実現されたネプロス、そしてKTC製品を今まで以上に自信を持っておすすめしていきたいと思います!
関連記事:KTC開発者インタビュー『壊れ方の美学』
関連記事:KTC開発者インタビュー
『壊れ方の美学』

京都機械工具株式会社(KTC)製品がなぜ、多くのユーザーから高い評価を受けているのか。その要因を知るため、商品開発部の坂根様と頼富様にエヒメマシンが独自インタビューを敢行しました。商品の企画から開発に至るまでの経緯や、壊れ方まで精密に計算され尽くした設計思想など、ここでしか聞けない貴重なお話を伺ってまいりました…
View Details